Stainless Steel End Cap Pn1.0 supplier
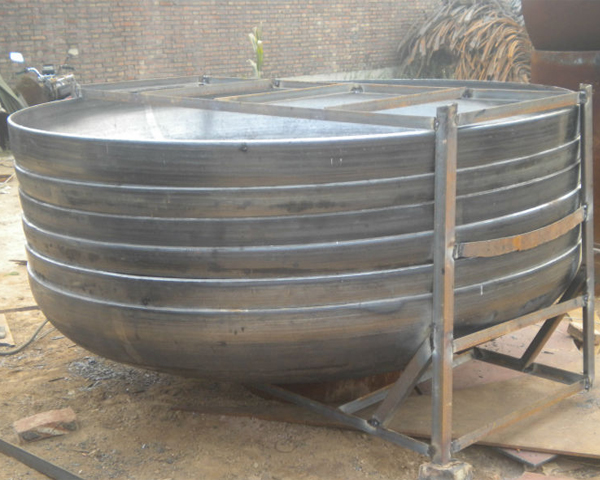
Size: | From 1/2" to 48" (Seamless pipe fittings). From 26" to 72" (Seam pipe fittings) |
Material | Carbon steel,Alloy steel,Stanless steel,Low-temperature steel,High performance |
Name: | Stainless Steel End Cap Pn1.0 supplier |
Standards: | ASME B16.9-2007, EN10253-1-1999, DIN2605-1-1992,JIS B2311-2009 JIS B2312-2009 |
Certificate: | API Q1-1958,ISO9001:2008,TUV,SGS,CCS,ETC |
Pipe cap including convex cap, conical shell, variable diameter section, the design of the flat cover and tighten.
Convex tube caps include: hemispherical tube cap, oval tube caps, disc pipe cap cap.From the standpoint of stress, convex cap in the gradually from hemispherical tube cap is not good, but look from the manufacturing difficulty, good manufacture gradually.
304 l stainless steel: 304 316 316 l, 321, 2520, 310, 316, such as material.
Size: DN15-48 ")
Wall thickness: SCH5 - SCH160
Standard: ASME DIN JIS BS GB/T, JB SH HG
USES: water, beverages, beer, food, petrochemical, nuclear power, chemical fertilizer, shipbuilding, machinery, medical equipment, waterproof processing, pipeline, etc
Packing: packed in wooden cases, cartons service: provide technical advice, installation guide, etc
Disc cap r, avoid joining together, will be thinned and high stress.
Splice weld direction when asked to only allow is radial and ring.After large cap may cancel this request.Stitching distance requirements, for more than 3 g, and not less than 100 mm (welding heat affected zone is high stress zone, and in the chemical composition of the area will be a loss. So to avoid the high stress area, the area and thickness. According to the practical experience, the stress attenuation length is greater than 3 g, and not less than 100 mm).But refrigeration equipment is difficult to meet the requirements, has its particularity.
Thebutt welds joining together after forming the head, should be 100% rays or ultrasonic testing, the qualified level with the equipment shell.Finally forming the same welding seam detection level, scale and equipment shell, high waste.
Example: if the shell is 20% testing equipment, qualified III.The straight stitching and final weld, III qualify, welded joint coefficient is 0.85;
So straight stitching, although 100% inspection, qualified level, along with the housing.
But must pay attention to the process manufacturing process:
The correct way is: blanking (line) - small plate together into a big board - molding - nondestructive testing
If it's wrong to do testing before molding, can't guarantee is qualified after forming.That is nondestructive testing refers to the nondestructive testing.